you are probably going to think I am nuts, but if you are using the manufacturer recommended temps, turn the temperature down... by a fair bit.
the stock Solidoodle hotend is not accurate as far as temps go - the placement of the thermistor is the reason why. Before swapping my stock hotend for the E3D, my temps were running about 40-45 degrees lower than most "recommended" temps. For PLA it was between 160-165C - not the 200-210C that most use. Overheating will also cause major "drooling".
There is a relatively simple way of calibrating for temperature using a very simple, single wall tall tower. (the single wall is achieved through slic3r settings - it is not modeled.)
using the attached temp calibration tower, which is 20mm x 20mm x 100mm tall (and can also be used for filament calibrations, just don't print the entire thing - kill the print at about 4-5mm tall) you will need to make a few adjustments in Slic3r print settings.
Layers and Perimeters
Layer Height
Layer Height: 0.2963 (not 0.3 - this is due to the use of a 5/16” threaded rod vs metric)
First Layer Height: can be same as above
Vertical Shells
Perimeters: 1
Spiral vase: unchecked
Horizontal Shells
Solid Layers - Top: 0, Bottom: 1 or 2
Quality - uncheck everything except “Detect Thin Walls”
Advanced
Seam Position: Nearest
External perimeters first: unchecked
Infill
Fill Density: 0
Fill Pattern: (should be greyed out)
Top/Bottom fill pattern: Rectilinear
If you have gone through the blog posts about calibration you should have the basics for this part down.
to do the temperature calibration, you will want to go ahead and slice the tower with the correct settings.
Once it has finished slicing, you will need to go into the g-code and do a bit of editing.
In RH, on the Preview window, there should be a tab that says "G-Code Editor" - click on that.
you should see something that looks like this:
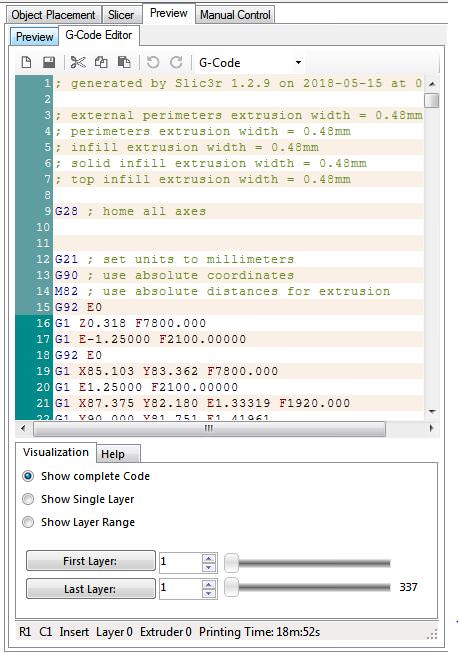
Dont be intimidated by it, yes it is a lot of code if you scroll through it, but it is actually pretty easy to navigate.
1st, decide how often you want to change temps - I would suggest every 15-20 layers
On a piece of paper, jot down layer heights that you want to change temps at...
Lets say every 20 layers, you want to change the temp 5 degrees Celsius, so your list will look something like this
1-20 - starting temp - 200C
21-40 - 195C
41-60 - 190C
61-80 - 185C
and so on...
Using the layer tool at the bottom of the screen, you can type in the layer you want in the "First Layer" box, then click the button (that says "First Layer" and it will jump to that layer in the g-code. Notice where the cursor is - that is the beginning of layer 21. Also note the color changes on the left side (alternating light green & dark green) - each time the color changes is a new layer.
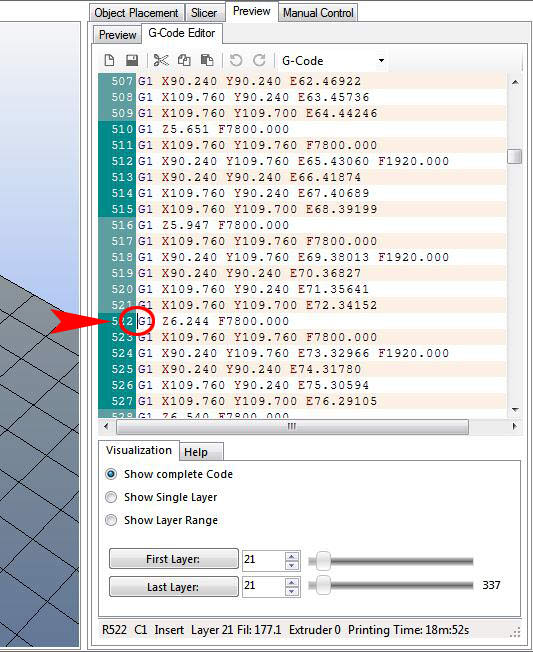
Now, click on the last line of the previous layer (at the end in empty space) to move the cursor up, then hit "enter" this will insert a new line for your temperature edit - should look like this at this point...
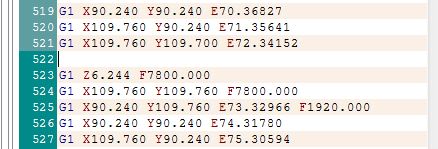
in that line type the following: M104 Sxxx (xxx is the temperature you want to change to - if you are starting at 200, this number would be 195, so your line would actually read M104 S195)
Note: you MUST use Capitol Letters when editing G-code, or it will not be read correctly.
repeat the procedure for each temperature change you want to make - enter the layer number you want, hit the button, add your temp edit.
when you have finished editing, you are ready to print, there is nothing else you need to do.. Set your starting temperature, heat up and hit the print button.. it should automatically change the temperature when it gets to the layers the temp changes have been added to.
If the temp gets low enough that the print starts to fail, kill it.
If the print finishes, remove it, and carefully look it over - you should be able to see where the temp changes occurred in good light.. you may want to mark the boundary of the temp changes with a marker so you can figure out which temp is best.
Test the layer adhesion by pulling at the layers.. if they separate easily, it is too cold. if they wont separate without serious effort, it is still to hot. It should take a little bit of effort to separate the layers.
If none of the temps seem right, repeat the process with new temp changes... starting with a lower temp than before and working your way down until you get it where it should be.
Post's attachmentstemp calibration tower.stl 1.06 kb, 2 downloads since 2018-05-15
You don't have the permssions to download the attachments of this post.
SD4 #1 & #2 - Lawsy carriages, E3D v6, Rumba controller board, mirror bed plate, X motor fan, upgraded PSU & Mica bed heater
SD4 #3 - in the works ~ Folgertech FT-5, rev 1
Printit Industries Beta Tester - Horizon H1